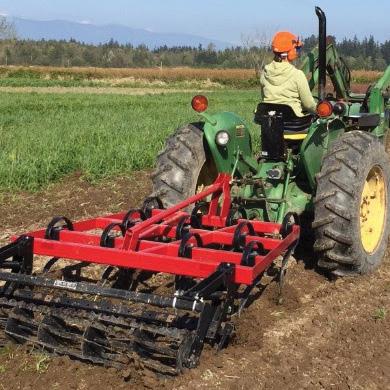
Farm Fund Grant Update: Viva Farms
In the 2016 grant cycle, the Co-op Farm Fund issued $8,000 in grants to seven inspiring proposals. If you tried your hand at playing the Farm Fund Game in the April Co-op News, you may recall the diversity of the funded projects. They tackled issues related to grazing management in a changing climate, formation of a new tool co-op, purchase and training for a multi-farm portable sheep shearing system, and four more innovative ideas. We are excited to watch these projects come to fruition in the coming year and to share their success stories with you.
One project that is already cultivating positive results is at Viva Farms, a nonprofit, small business farm incubator located in Skagit Valley. Its mission is to support aspiring and limited-resource farmers to overcome barriers to farm ownership by providing bilingual training in holistic and organic farming practices and management, and much needed access to land, infrastructure, equipment, marketing, and capital.
Started in 2009, Viva Farm’s mission is to launch a new generation of farmers.
Viva Farms received a Co-op Farm Fund grant to purchase a new field cultivator. The implement was purchased from Farmer’s Equipment Co. in Lynden where the farm received a nonprofit discount, further leveraging its Farm Fund grant. Hooray for local businesses!
Several farmers at Viva have already had great success using the new field cultivator, which prepares soil for planting without the need for rototilling. Rob Smith, Viva Farms operations and incubator director, described the cultivator as “a missing link in our ‘toolkit’ that allows us to work up a field in a more efficient, timely, and sustainable manner.”
Efficient because the field cultivator is much faster to use in the field, and with fewer mechanical parts, it is less likely to break down and requires less maintenance. All these factors result in less downtime in the field, fewer costly repairs, and overall labor savings.
Sustainable because it is gentler on the soil structure, known in farmer lingo as the “tilth.” A rototiller, on the other hand, can create soil compaction or pulverize the soil resulting in hardpan that impairs drainage and plant growth. Also, because rototillers are powered implements, they use more fuel to operate than the cultivator that is simply pulled behind a tractor.
This improvement in efficiency and sustainability allows farmers more time to, well, farm, and will hopefully result in greater productivity and eventually more deliveries of local food to the Co-op’s produce departments. Throughout the growing season Viva, and the 14 independent farmers currently working the land and sharing equipment with Viva, provide certified organic vegetables, herbs, and berries to the Puget Sound Food Hub, which serves many Whatcom County food businesses.
In the same way that the Co-op is committed to the principal of cooperation among cooperatives, the farmers on-site at Viva Farms are building community and learning from each other. Rob said: “Despite working on their own independent operations, the farmers help support each other for success. This all happens across language and cultural barriers—finding out what is shared between all farmers, and all humans, really.”
For the first time, Viva Farms is at 100 percent capacity and will look into expanding in 2017. Rob wants to spread the word about what Viva Farms is accomplishing, and tell people that it wouldn’t be possible without the farmers and a network of community partners.
That network includes every Co-op shopper who has contributed to the Farm Fund and chooses to purchase local produce from the Co-op—Whatcom County’s only community-owned grocery store.
Learn more at vivafarms.org